Sculpting with steel: The art of blacksmithing
Blacksmithing is hot work.
It’s hard work.
It’s lifting a three-pound hammer 150 times in a row.
For Jason Purdy, it’s also an art — and it’s awesome.
“Blacksmithing has more in common with sculpting than anything,” says Purdy, Academic Chair, Ironworker, Crane and Hoist, Recreation Vehicle Service Technician and Railway Conductor. “In blacksmithing, you’re manipulating metal. You’re not removing material like a machinist or adding material like a welder. You’re forging, shaping the material.”
Whether the word blacksmith conjures an old-timey image of a guild craft essential to daily life or a modern vision of an artisan knife maker competing on TV show Forged in Fire, the work of a blacksmith is a showcase of technology built on tradition.
Although industrial trades such as machining and welding largely replaced the traditional role of the blacksmith, the craft remains very much alive.
There are still elements of blacksmithing present in industrial training and apprenticeships, things like heat treating procedures and the science of carbon content and alloy steel.
🔨 Moving metal
According to Purdy, if you can swing a hammer you can try blacksmithing. But don’t be fooled, there’s a skillset that comes with the physical aspect of moving metal.
“You’re not just driving nails,” says Purdy. “There’s a skill to moving metal, forming, striking, having the angles the right way — and it’s a learned skill. Practice is everything.”
Jason Purdy teaching the angles of moving metal.
You also need to have a plan for what you’re going to build, what the form is going to be. Then it’s a matter of tools and talent.
“At the most rudimentary level you can dig a hole in the ground and build a fire, get a piece of steel and two hammers and away you go,” says Purdy.
The blacksmith lab at SAIT’s Crane and Ironworker Facility at the Point Trotter campus has much more to offer than that.
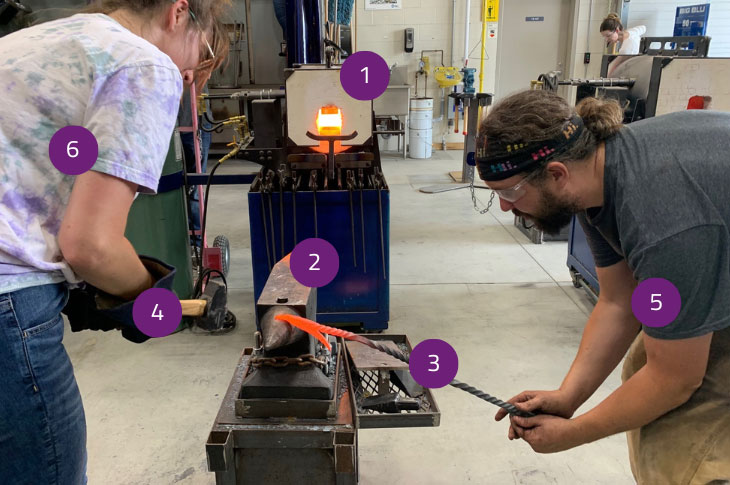
Inside the shop, the talent of the smith matters as much or more than the tools.
“On an episode of Forged in Fire, one guy — Ryu Lim, who’s an ironworker — had an old satellite dish rigged up as a homemade forge and his competitor had hundreds of thousands of dollars’ worth of equipment in his shop. Lim won with the satellite dish,” recalls Purdy.
“It’s more about talent than tools — talent, interest, care and invention.”
💪 Mentors with muscle
A journeyman welder and millwright, Purdy’s love of the art of blacksmithing began about 20 years ago. When the last certified blacksmith at the Sullivan Mine in Kimberley, B.C. retired, he took over.
“I walked into his shop and it had all the original tongs and forges. I thought, ‘this is cool’, and it was something that interested me as a tradesperson. After all, blacksmithing was the original welder/millwright.
“I started hammering and fell in love with it. I built my own forge, because at that time you couldn’t buy one. Then, when they decommissioned the mine in 2002, I bought a bunch of the tools, including a 250-pound anvil — it’s probably 150 years old.”
These days, Purdy’s focus is mostly knifemaking. He likes things old school and can put between 20-30 hours into a knife.
“I refuse to use jigs and go into mass production — to me it’s an art. When I make something as a gift, I think about the person it’s for all the time during the process.”
To start forging steel, Purdy recommends taking a course to ensure you’re working safely, especially if you’re new to a shop environment.
From his experience working with students, the appeal of the craft is tied to the satisfaction of building something.
“They’re sweaty and covered in soot and dust, but you can see the pride they have in the work they’ve built, in having made something with their hands,” says Purdy. “There’s a lot of satisfaction in that – it’s highly rewarding.”
Blacksmithing at SAIT
If you’re looking to try your hand — and hammer — at sculpting with steel, SAIT offers a course through the Centre for Continuing Education and Professional Studies throughout the year. Register now for courses starting Oct. 24 and Nov. 14.
Learn moreLearning for Life
We prepare students for successful careers and lives.
SAIT'S
2020-2025
Strategic plan
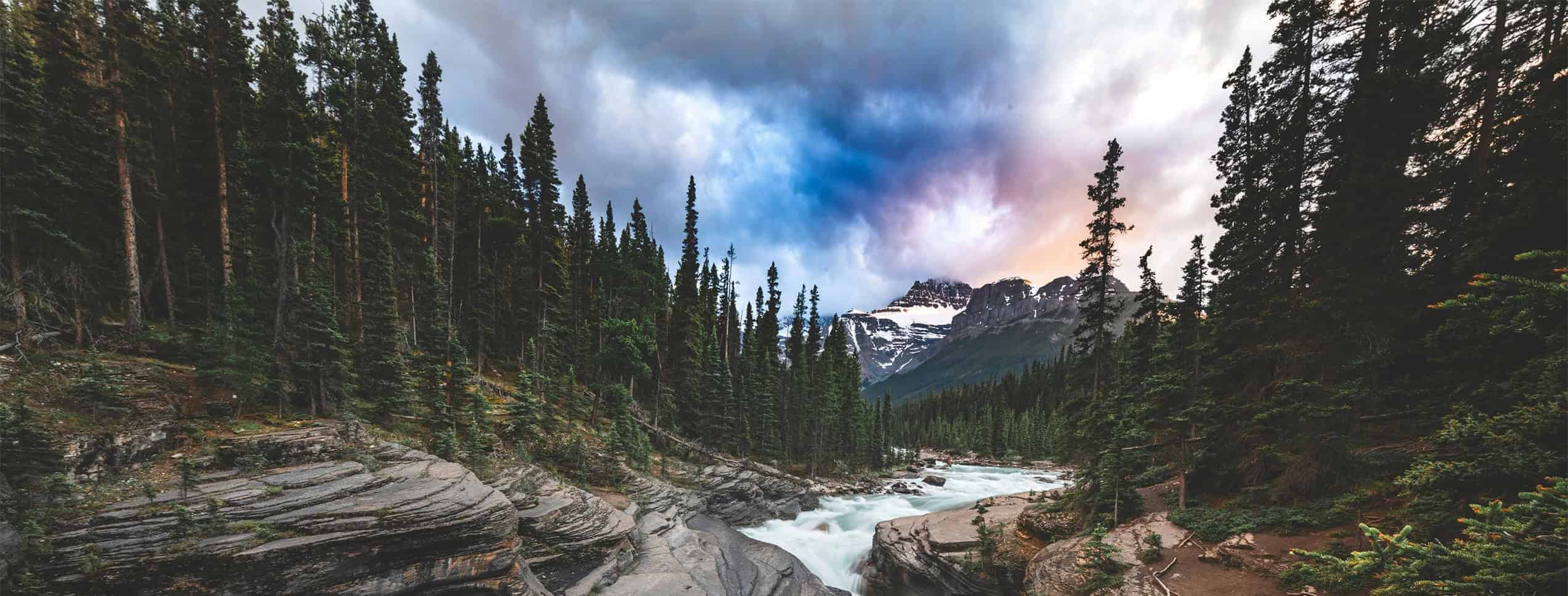
Oki, Âba wathtech, Danit'ada, Tawnshi, Hello.
SAIT is located on the traditional territories of the Niitsitapi (Blackfoot) and the people of Treaty 7 which includes the Siksika, the Piikani, the Kainai, the Tsuut’ina and the Îyârhe Nakoda of Bearspaw, Chiniki and Goodstoney.
We are situated in an area the Blackfoot tribes traditionally called Moh’kinsstis, where the Bow River meets the Elbow River. We now call it the city of Calgary, which is also home to the Métis Nation of Alberta.